High conductivity and a high melting point are just a few of iridium’s unique properties. Above all, iridium serves as an excellent catalyst for Proton Exchange Membrane (PEM) water electrolysis. So much so, that virtually all PEM electrolyzers in use today depend on iridium as a catalyst for the Oxygen Evolution Reaction (OER) on the anode side of their cells. There are, however, some drawbacks with this approach.
Iridium also happens to be one of the rarest elements on Earth. In fact, it’s over 50 times rarer than gold. And with only 7 to 9 tons mined annually, its labor-intensive extraction adds to an already tense environmental impact. This is because iridium’s extraction and refining processes are highly CO₂-intensive, further complicating its use in alternative energies.
The cost of iridium adds yet another layer of complexity to its use in hydrogen generation. As one of the rarest and most expensive precious metals, prices fluctuate between 4,000 and 6,000 US-$ per ounce. As such, iridium’s limited supply poses a challenge to scaling renewable hydrogen production. Its scarcity, combined with the high demand for PEM electrolyzers, drives up costs. And with the iridium loading of the anode side of these systems requiring 1 to 2 mg/cm² this dependency makes iridium reduction not just a technical priority but a critical step toward making hydrogen an economically viable energy solution.
As global demand for electrolyzers rises, the reliance on iridium presents a growing challenge. Iridium is a byproduct of platinum refining, hence both markets are interlinked. Increased adoption of iridium-dependent technologies only heightens its scarcity, making reduced dependency critical for the sake of hydrogen generation scalability and sustainability. Additionally, if the market for internal combustion engine (ICE) vehicles declines in the long term, the supply of platinum (and consequently iridium) may decrease, as the primary market for platinum today is in catalytic converters for ICE cars and trucks. However, efforts to optimize iridium usage are well underway, ensuring the hydrogen industry’s ability to meet future demand without the constraint of rare resources.
But as the global demand for iridium-based hydrogen technology grows, the element’s scarcity will only increase. This further highlights the critical efforts of reducing iridium usage to ensure affordability, scalability, and sustainability. And, to meet need, collaborative efforts to reduce dependency on such an elusive metal are well underway.
PEM electrolyzer technology
PEM electrolyzers are used to produce hydrogen through water electrolysis, a process responsible for splitting water into hydrogen and oxygen using electricity. These electrolyzers are used for green hydrogen production, supporting a wide array of applications such as steel manufacturing, transportation, and chemical production. The electrolyzer is made up of multiple components, including the anode, membrane, and cathode, to name a few. However, it’s the anode that becomes a bottleneck in this process.
Despite its critical role in facilitating the oxygen evolution reaction (OER), the anode’s dependence on high iridium loadings remains a persistent challenge. Because of its excellent corrosion resistance, conductive properties, and high activity for the OER, iridium is relied upon by PEM electrolyzers as a critical element of the anode catalyst.
The Membrane Electrode Assembly (MEA) is at the heart of a PEM electrolyzer. It’s at this point in the process where water is split into hydrogen and oxygen ions through electrolysis. In fact, the MEA’s design is crucial for efficiency, ensuring effective proton transfer, minimal energy losses, and durability under harsh conditions. By optimizing catalyst usage and enhancing material performance, modern MEA technologies are paving the way for scalable hydrogen production. Making renewable hydrogen an increasingly viable solution for decarbonization.
The components of the PEM electrolyzer are dependent on one another for optimal functionality and hydrogen production. Given the reliance on such a precious element, iridium-reducing technology succeeds by optimizing iridium usage to enhance the PEM hydrogen generation process. And a growing urgency to reduce reliance on iridium for financial and environmental gain has sparked innovation within the hydrogen community. For PEM electrolyzers, this meant developing new component technology to minimize the impact of scarce materials while maintaining optimal performance.
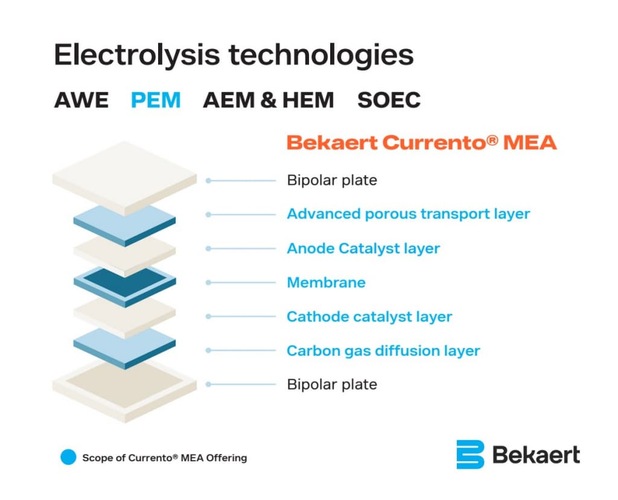
Fig. 2: MEA stack
A partnership built on progress
The demanding operating conditions of the PEM electrolyzer present unique challenges, particularly in terms of material degradation over time. With durability being such a critical factor, iridium’s inherent resilience has long made it a key component. However, as hydrogen production scales up, reducing iridium use becomes essential. But providing solutions to these types of challenges requires innovation and collaborative efforts.
In 2017, Toshiba began developing innovative iridium reducing MEA technology that decreases the cost of the catalyst and increases the surface area. In turn, this reduces iridium loading by up to 90 percent. By moving away from Coated Catalyst Membranes (CCM) to direct coating onto a Porous Transport Layer (PTL). This results in a significant reduction of iridium use in hydrogen generation.
By 2022, Toshiba partnered with Bekaert to transform the availability of Toshiba’s MEA technology. And, in 2024, the companies entered into an official licensing agreement, thereby enabling Bekaert to scale up Toshiba’s technology. Bringing innovative, cost-saving technology to the market.
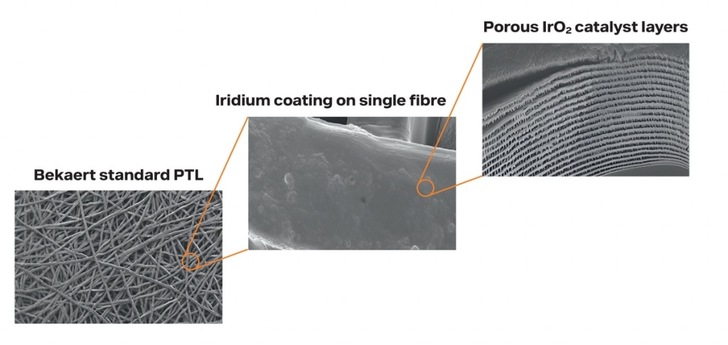
Fig. 3: Clos-up view
Innovating sustainable components
Sustainability is deeply embedded in every stage of Bekaert’s innovative processes. Ensuring that every solution is developed to meet or surpass customer needs, while also contributing to a more sustainable future for the planet. And the reduction of iridium consumption, in partnership with Toshiba, exemplifies Bekaert’s commitment to sustainability. Tackling not only the environmental implications of rare metal extraction, but also the economic pressures tied to iridium’s scarcity.
Shaping the future of hydrogen
As the energy sector pivots toward cleaner alternatives, innovations like iridium-saving PEM-MEA technology are vital to ensuring that PEM electrolyzers remain both practical and scalable. By embracing advanced engineering and collaborative breakthroughs, Bekaert is setting a new standard for sustainability without compromising durability or efficiency. This approach positions hydrogen technology as not just a solution for today’s energy demands, but a cornerstone for a cleaner, more resilient future.
Author: Lowie D’Hooghe, Bekaert, Zwevegem, Belgium, lowie.dhooghe@bekaert.com